Why Your Struggle in Hiring Skilled Welders is Holding Your Welding Projects Back
Skilled welders’ key role includes effectively joining metal components in construction, manufacturing, and industrial development projects. This is part of their essential practice in making sure buildings, machines, and infrastructure are strong and safe.
Can you guarantee that you can find the right candidate right away?
If you’re an HR manager in the welding industry, hiring skilled welders helps your projects meet safety and quality standards. However, you’ve likely faced the same challenge over and over: finding qualified welders who are not only skilled but also reliable, safe-compliant, and ready to work.
The truth is, traditional recruitment methods aren’t working anymore. Thus, relying on outdated hiring practices often leads to project delays, higher labor costs, and worse, lower work quality. Skills gap in welding is more than just a hiring problem—it slows down business growth. But the good news is, the solution is already within reach.
Read this blog and learn how partnering with a certified welding training center can make it easier for you to hire skilled welders.
Table of Content
- What is a Skilled Welder?
- Why It’s Hard to Hire Skilled Welders in the Welding Industry Today
- Skilled Welders Shortage in the Philippines
- Top 5 Common Challenges in Hiring Skilled Welders
- Lack of Industry Expertise
- No Existing Welding Certifications
- Defiance with Standard Safety Protocols
- Poor Work Ethics
- High Turnover Rates Among Welders
- Conclusion
What is a Skilled Welder?
A professional in joining metal components to ensure the structural strength of buildings, machinery, and infrastructure projects. These are professionals who have completed formal welding training and apprenticeships, earned welding certifications, and mastered various welding equipment techniques. They also continue to upskill, allowing them to adapt to new technologies and apply them in their work.
Why It’s Hard to Hire Skilled Welders in the Welding Industry Today
If you are currently working in recruitment for the welding industry, you have probably experienced the impact of the ongoing welder shortage—but ever wonder what’s causing your recruitment bottlenecks? It’s the shortage of skilled welders.
Skilled Welders Shortage in the Philippines
The shortage of skilled welders in the Philippines is part of a global trend. Similarly, a recent study revealed the average age of welders is 55 years old. This means that many experienced welders are reaching retirement age, but only fewer young workers are entering the welding industry.
Top 5 Common Challenges in Hiring Skilled Welders
Knowing the challenges hiring skilled welders entail will help you identify the calculative steps that you should take before deployment. As a result, you won’t have to waste time and resources in onboarding welders who may not meet project expectations.
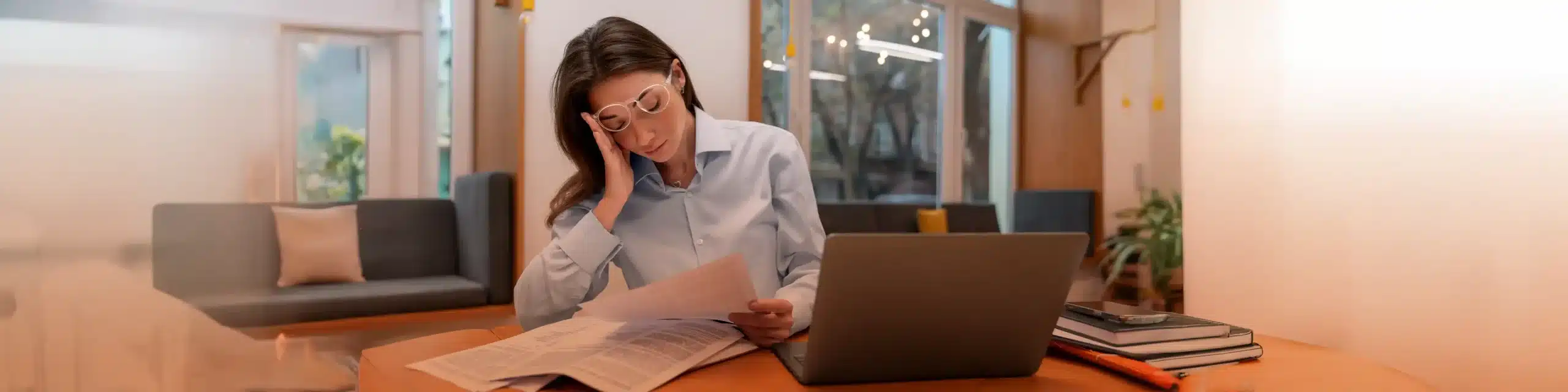
1. Lack of Industry Expertise
As the welding sector improves, new equipment, techniques, and methods are continuously introduced to develop strong and durable structures. This creates a dynamic environment where the demand for skilled welders becomes prominent.
However, inconsistent skills and the lack of hands-on training make recruitment a tedious process. This is especially true when their skills or traits don’t fully meet the needs of the project.
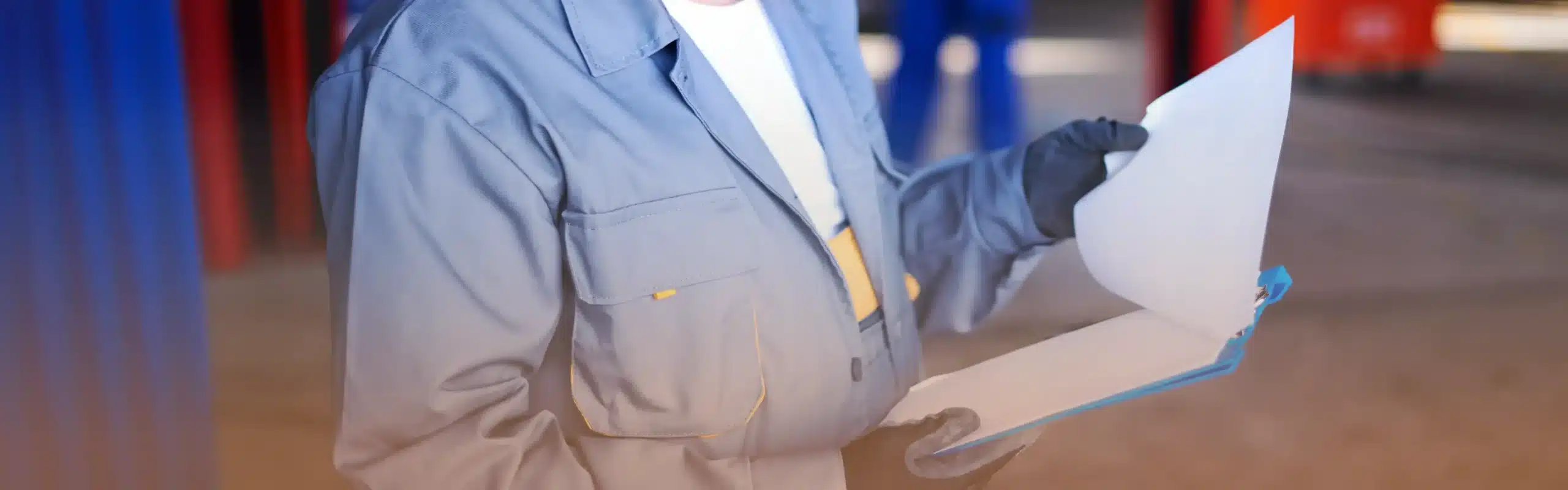
2. No Existing Welding Certifications
Why does hiring a certified welder matter? Well, while welding doesn’t necessarily require a formal education to get started, the absence of certifications makes a welder unqualified.
Keep in mind that without local or global certifications, it will be hard to prove their skills and expertise.
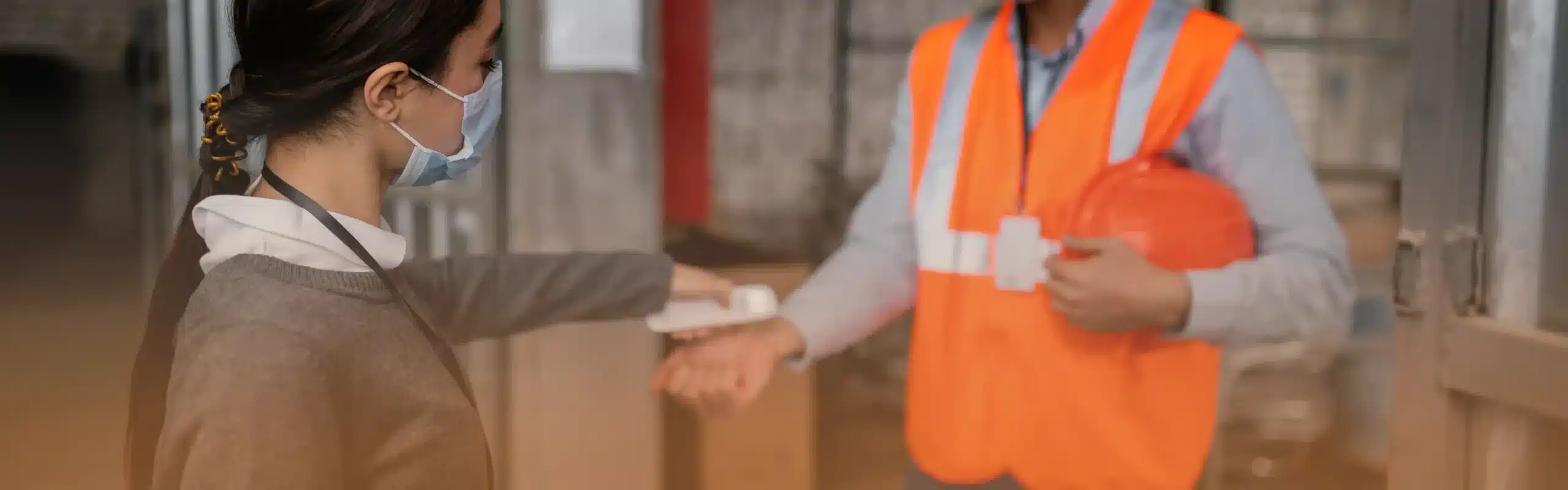
3. Defiance with Standard Safety Protocols
Welding is a physically demanding blue-collar job that can be extremely dangerous without proper safety training, equipment handling knowledge, and strict compliance with standard safety protocols
Did you know?
Rig Welders and Underwater Welders are among the highest-paid welding professionals due to their working conditions. They earn as much as $40,000 to $200,000+ in a year. That’s equal to 2 million to 11 million in Pesos!
Failing to protect welders from hazards—such as toxic fumes, burns, and electric shocks—can lead to serious health problems at work. That’s why they need to receive proper risk awareness and safety training to prevent accidents that could endanger their lives.
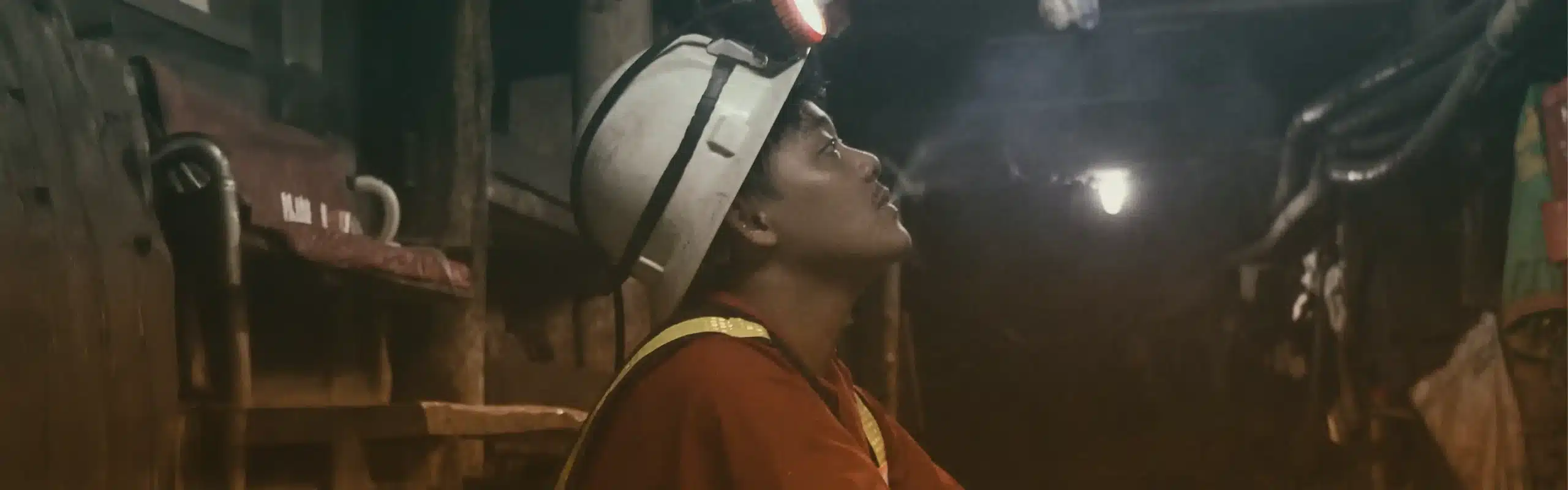
4. Poor Work Ethics
Reliability issues and lack of professionalism among welders often lead to project delays and cost overruns. These problems can trigger several negative consequences:
Structural Failures
When welders are distracted or inattentive, the quality of their work suffers. Poorly welded joints are a major reason why some buildings and bridges collapse. Remember, properly welded metal joints are essential to a structure’s overall integrity.
Equipment Mishandling
Failing to conduct welding equipment maintenance leads to tool malfunctions and unexpected hazards. This not only puts workers at risk but also causes operational downtime and delays in project completion.
Loss of Client Trust
A failed welding project can damage a company’s reputation. When clients lose confidence, it can result in lost partnerships and fewer chances for repeat business.
Increased Workplace Accidents
Poor work habits often come with a lack of attention to safety protocols. This raises the risk of accidents, including injuries and long-term health issues caused by exposure to harmful fumes.
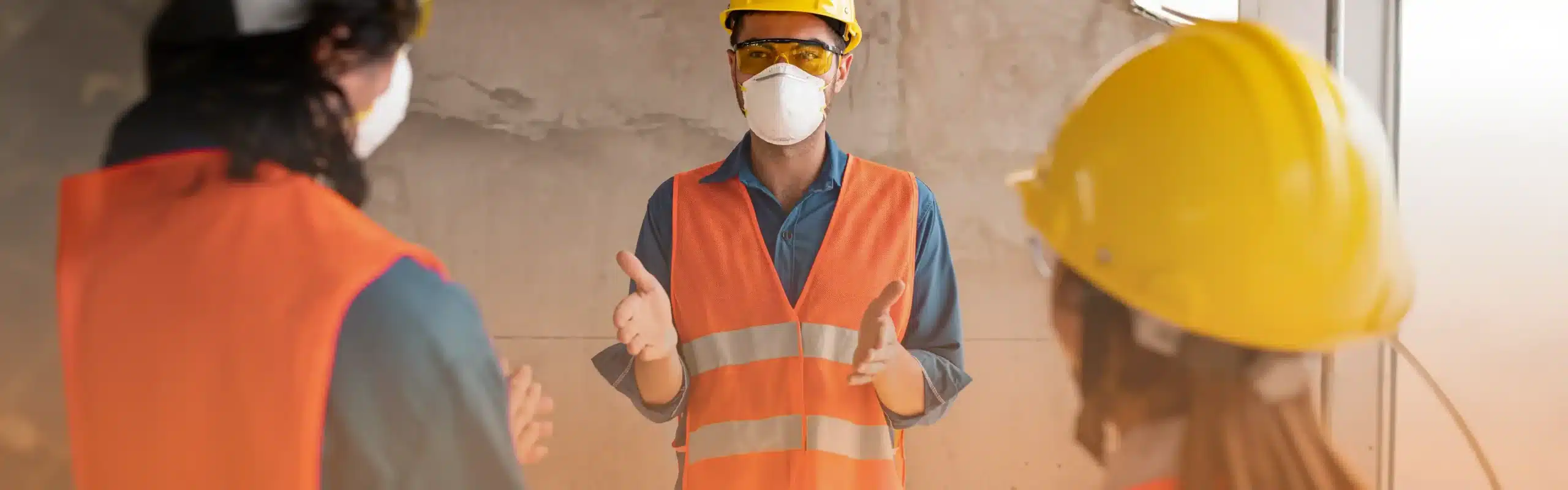
5. High Turnover Rates Among Welders
High turnover from poor candidate-job matching can interrupt training and knowledge transfer, leading to more mistakes and low-quality welds. But, partnering with a certified welding training center like TOTC helps you hire skilled, job-ready welders and reduce these risks.
TOTC’s Welding Training Center is a Proven Welder Recruitment Solutions for Your Business
TOTC directly addresses the welding recruitment shortage by offering world-class welding training designed for both local and international standards.
Here’s how we make a difference:
- Accredited Testing Facility
Through advanced training programs, at TOTC, we equip welders with the skills needed to meet employer expectations in manufacturing, shipbuilding, construction, and oil & gas—both locally and abroad. - Certified and Job-Ready Candidates
Our certified welders hold internationally recognized credentials, possess hands-on experience, and demonstrate technical skills that align with strict safety and quality standards. - Pre-Screened, Reliable Talent Pool
All TOTC welders are thoroughly evaluated for skills, reliability, discipline, and long-term employability—key qualities that a recruitment manager like you value and trust. - Employer-Driven Training Programs
At TOTC, we collaborate closely with employers to understand their specific needs—aligning our training programs to match real-world job demands and ensure workforce readiness.
Conclusion: Why Hiring a Skilled Welder Matters
Finding qualified welders with the right certifications and hands-on experience is a growing challenge for many recruitment managers. The ongoing labor shortage in the welding industry makes it even harder to fill urgent roles. When this happens, your welding projects face delays, costs go up, and clients lose confidence.
But you can always overcome this by partnering with a trusted welding training center like TOTC. By doing so, you can gain direct access to certified, job-ready welders. This saves your time, lowers hiring risks, and helps you meet welding project deadlines with confidence.
Ready to Hire Certified Skilled Welders?
TOTC’s hands-on welding training programs ensure every candidate is equipped with the right welding skills, safety knowledge, and certifications your welding projects need to succeed.
HIRE SKILLED WELDERS WITH TOTC